Blue Origin has teamed up with Auburn University’s National Center for Additive Manufacturing Excellence (NCAME) to push the boundaries of 3D printing with copper. Jeff Bezos founded Blue Origin, which is a pioneering aerospace company. This collaboration aims to tackle the material’s unique manufacturing challenges. It opens new possibilities for aerospace and advanced manufacturing.
Blue Origin’s Donation to Support Copper Research
Blue Origin donated two
EOS M290 powder bed fusion (PBF) 3D printers to NCAME. These industrial-grade printers are specifically designed to handle high-performance materials. This makes them ideal for advancing research into copper’s additive manufacturing capabilities.

This donation complements the two EOS M290s NCAME already owned, doubling their capacity to conduct applied research tailored to Blue Origin’s needs.
The Challenges of 3D Printing Copper
Copper's high reflectivity and thermal conductivity make it particularly difficult to 3D print using traditional laser-based systems. Much of the laser energy reflects off the copper powder, leading to inefficient melting and inconsistent results. Once melted, copper’s absorptivity increases, creating unstable melt pools and potential defects in the final print.
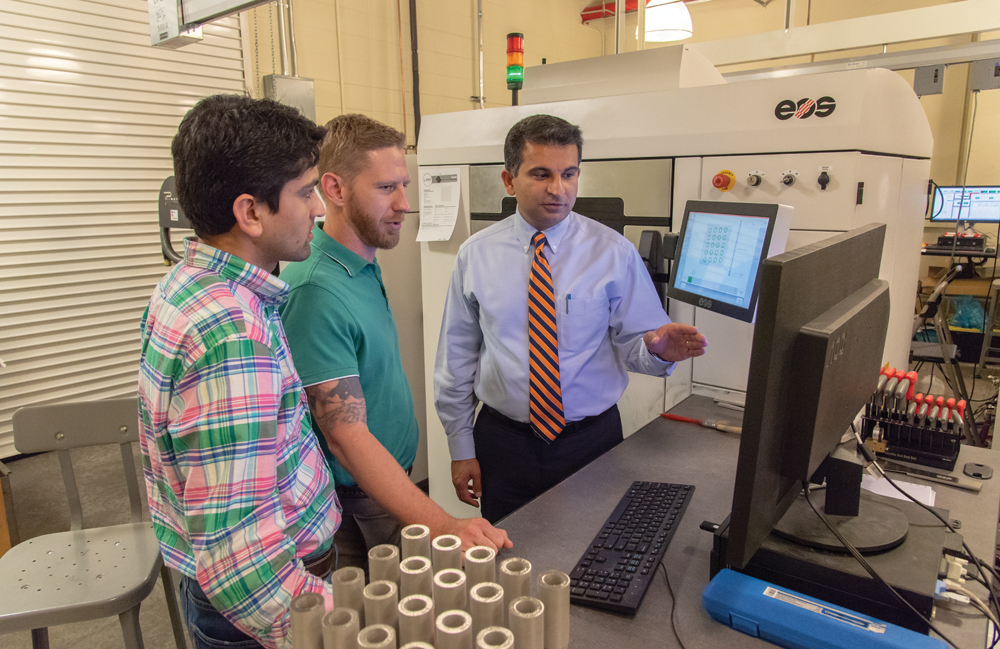
According to NCAME Director Nima Shamsaei, “Copper’s properties present major challenges for traditional laser-based 3D printing systems to effectively melt and fuse the powder.”
Research scientist Jonathan Pegues added that specialized lasers are often needed to overcome these issues.
However, alloys, like copper-chromium-niobium (GRCop-42) — originally developed by NASA — have demonstrated successful printing with the standard infrared fiber (IRF) lasers in the EOS M290 printers.
Paving the Way for Aerospace Innovation
Blue Origin’s interest in copper 3D printing links directly to its mission to develop reusable rockets and other advanced space technologies. Copper’s excellent thermal and electrical conductivity makes it ideal for rocket engine components, including combustion chambers and heat exchangers. By refining copper printing techniques, Blue Origin aims to create more efficient, lightweight, and durable parts for its next-generation vehicles.

This partnership also strengthens Auburn University’s long-standing involvement in aerospace and additive manufacturing research. Auburn has collaborated with NASA for over a decade. They keep contributing to advancements in materials science and manufacturing processes. The NCAME research team now works alongside Blue Origin to accelerate the development of copper alloys.
Recent Blue Origin Milestones
In January 2025, Blue Origin successfully launched its first orbital rocket, New Glenn, from Cape Canaveral Space Force Station. This marked a significant milestone for the company, positioning it as a key player in the evolving space industry.

Additionally, Blue Origin recently announced the 11th crewed mission of its reusable suborbital rocket,
New Shepard. This flight will feature an
all-female crew, including former NASA scientists and pop icon
Katy Perry — a move that highlights the company’s commitment to expanding access to space.
The Future of Copper 3D Printing
The Blue Origin-Auburn University partnership highlights the growing importance of additive manufacturing in the aerospace sector. By overcoming copper’s complex printing challenges, the collaboration could pave the way faster. Moreover, the cost-effective production of critical rocket components and other high-performance systems is possible by this partnership.

With continued innovation in copper alloys like GRCop-42 and improvements in laser technology, this research may also benefit industries beyond aerospace — including
energy,
electronics, and
defense.
Could copper 3D printing be the next big breakthrough in aerospace manufacturing? Share your thoughts in the comments!